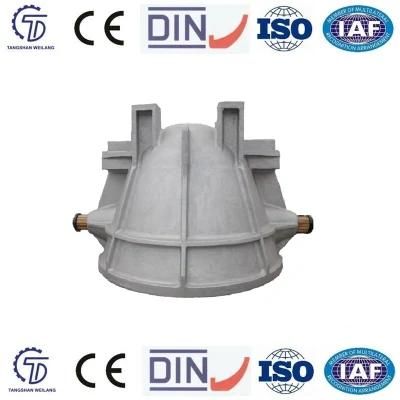
Mining Machine Parts of Slog Pot
Tangshan Weilang Trading Co., Ltd.- Casting Form Usage Count:Permanent
- Casting Metal:Cast Steel
- Casting Form Material:Sand
- Casting Method:Sand Casting
- Surface Treatment:Sand Blast
- Surface Roughness:Ra12.5
Base Info
- Exhibition:We Always Attend Some Exhibition in Abroad.
- Plant:We Have Our Own Factory
- After Sales Service:Engineer Available to Service Machinery Overseas
- Our Goal:to Provide Top-Quality Products and Service
- Specifications:High Dimension Accuracy, Wear Resistance
- Use:Used for Metal Casting
- Our Customers:Russia,Turkey, Bangladesh, Columbia,Vietnam
- Our Advantage:Rich Experience, Best Service, Professional Team.
- Product Application:Metallurgy Smelting in Steel Works
- Certification:CE, ISO 9001:2000, ISO 9001:2008
- Standard:GB,AISI,DIN,GOST
- Machining Tolerance:+,-0.01mm
- Coating:Rust and Heat Resistant Coating
- OEM:We Can Also Accept The Trail Order.
- Transport Package:Seaworthy Package
- Specification:According to the client
- Trademark:Weilang
- Origin:China, Hebei
- HS Code:84542090
- Production Capacity:100000 Tons Per Year
Description
Normalized, Normalized and Tempered, Quenched and Tempered
Machining
Rough machined, Semi-finished machined, Finished machined
Non-Destructive Testing
Magnetic Particle Testing, Ultrasonic Testing, Penetrant Testing
Design
Slag pots are crucial items as they are part of lifting equipment and therefore undergo in terms of mechanical design engineering and handling the national safety regulations of the state where they are supposed to be operated. Thus, the following design criteria must be taken into consideration:
Type of furnace that the slag pot will service,
Quantity and type of slag generated,
Method of handling and dumping the pot,
Heat impact during operation,
Dimensional restrictions,
Pot maintenance procedures
Slag pots designed by OEM comply with the requirements of structure dimensions, mechanical properties and guarantee by chemical composition, heat treatment, non-destructive testing and visual
inspection against surface.
Every slag pot we produce is designed and engineered to meet specific and critical custom specifications. Our pots can be filled to capacity with up to 1649º C slag. Our expert engineering and casting technicians are committed to working with you to suggest modifications that reduce cost and extend pot life through improved efficiencies.
Our slag pots are utilized in many applications including BOFs, AODs, Electric Arc and Blast Furnaces, and nonferrous refineries for the melting of magnesium and copper nickel smelting.
Product Display
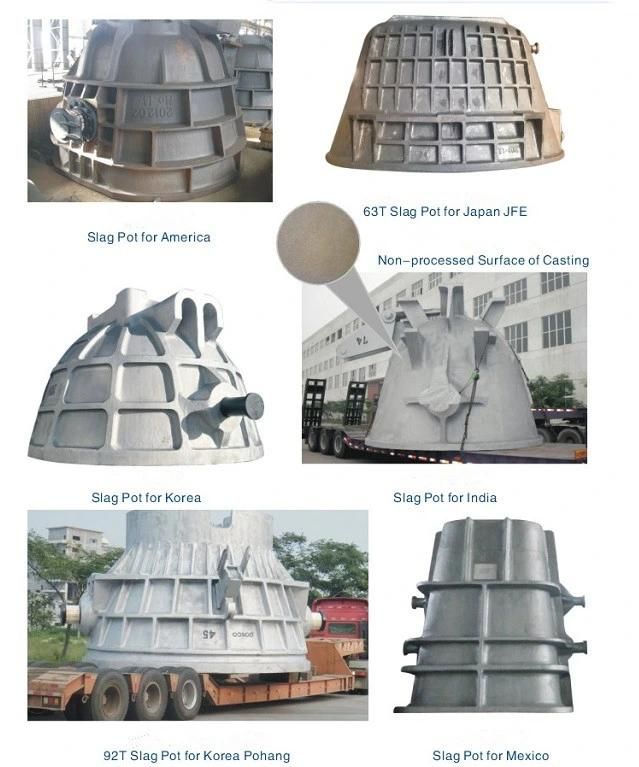
Production Process
1. Wooden pattern Production
2. Molding
3. Pouring
4. First cleaning
5. Heat treatment - grinding (inspection)
6. Rough machining (inspection)-finishing machining (inspection)
7. Packing-delivering
Production Equipment
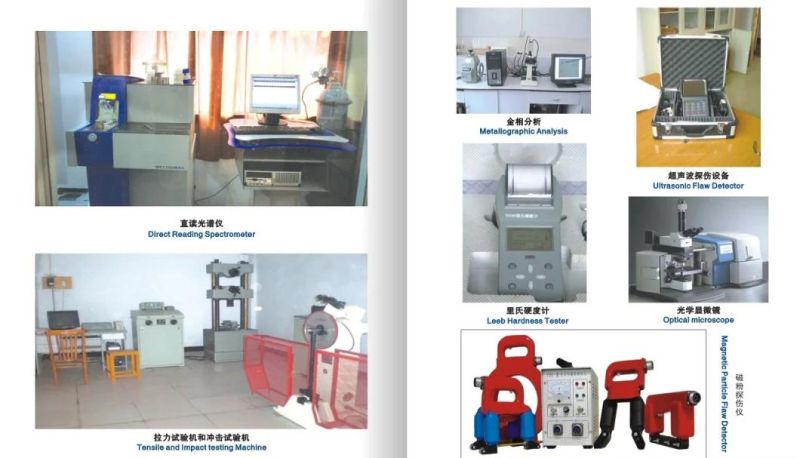

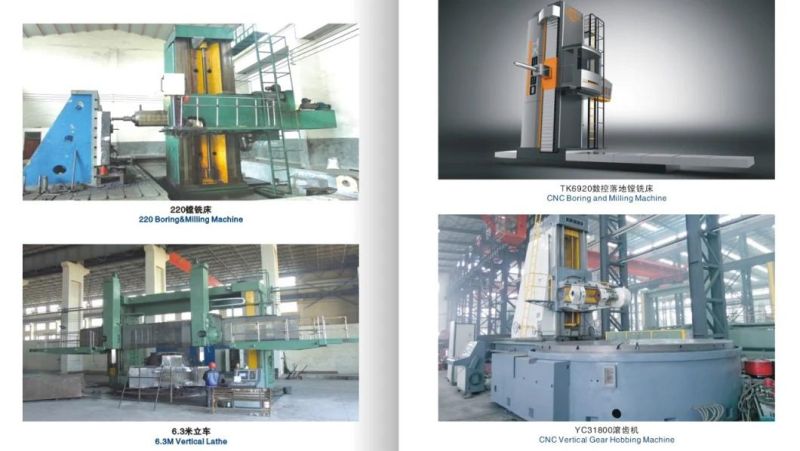
Sales Record
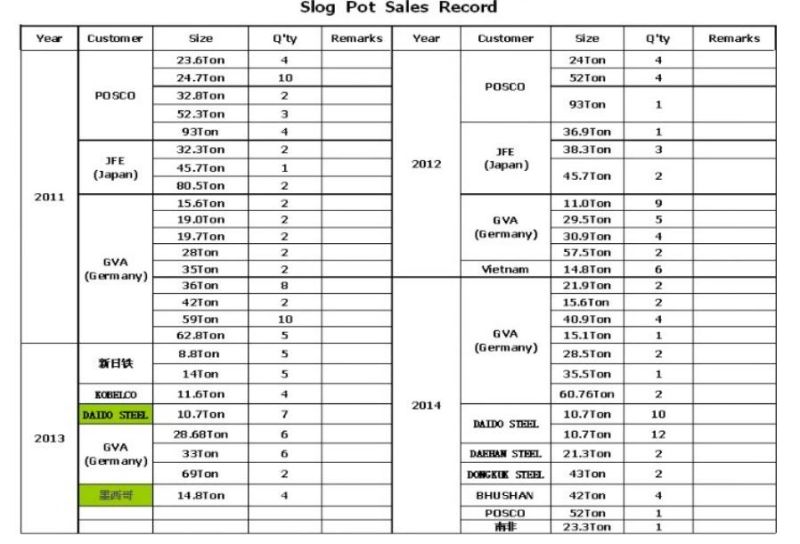
Delivery
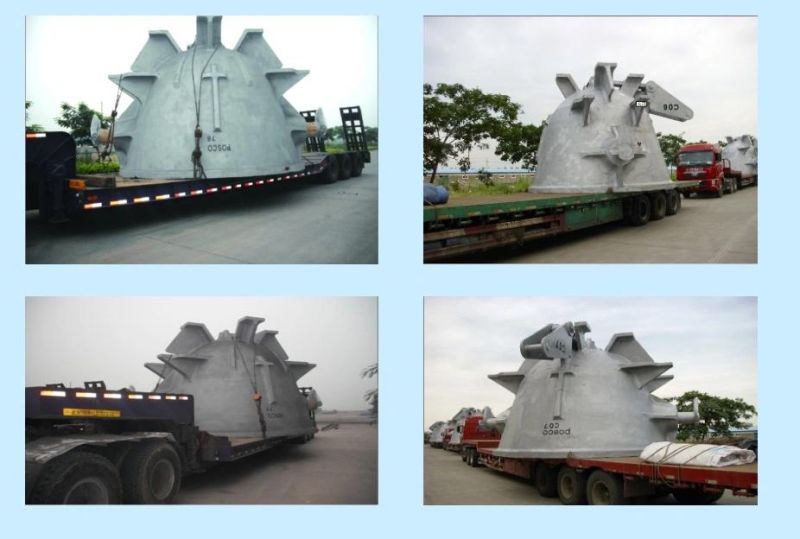
Slag pots are available with capacities of 30 - 1050 cubic feet. Finished weights range from 1.5 Ton to 120 Tons. Our facilities have the capability to cast pots in nearly every shape and style for a variety of mounting systems and methods of transport.