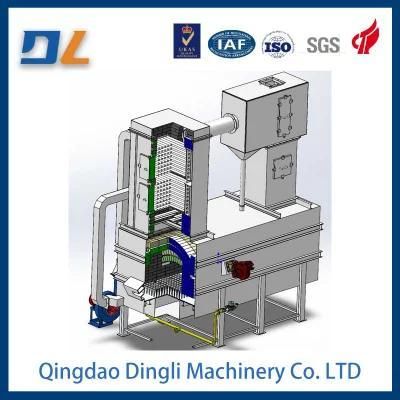
Regeneration of Old Sand Culture Furnace by Thermal Method
Qingdao Ding Li Machinery Co., Ltd.- Casting Method:Sand Casting
- Casting Form Material:Sand
- Casting Metal:Cast Steel
- Casting Form Usage Count:Permanent
- Surface Treatment:Electroplating
- Surface Roughness:Ra0.1
Base Info
- Coating:Water
- Machining Tolerance:+,-0.01mm
- Certification:ISO 9001:2000, ISO 9001:2008
- Transport Package:Custom
- Trademark:DL
- Origin:Qingdao
- Production Capacity:100
Description
Basic Info.
Coating Water Machining Tolerance +/-0.01mm Certification ISO 9001:2000, ISO 9001:2008 Transport Package Custom Trademark DL Origin Qingdao Production Capacity 100Product Description
Brief introduction of structure and working principle of thermal regenerative roasterThis part includes three parts: sand preheater, roaster and cooling bed.
1. Sand preheater
The body is a vertical box body with a buffer board inside. The hot flue gas from the roaster passes from top to bottom through the sand preheater and then into the adjacent air preheater, where the old sand discharged from the feeder falls freely from top to bottom and enters the roaster after preheating.
2. Baking oven
It consists of roasting furnace body, boiling air supply system and combustion system.
(1) Furnace body: the shell is a welded box body, separated into two upper and lower chambers. The upper chamber is a boiling chamber, the lower chamber is a bellows, and the middle bed plate is equipped with a hood. The boiling chamber is surrounded by firebrick and lined with aluminum silicate fiber. One end of the furnace body is provided with a sand recovery inlet, the other end is provided with a discharge port.
(2) Boiling air supply system: it is composed of fan, disc valve, air preheater and hot and cold air duct.
(3) Combustion system: it consists of two sets of combustion devices. Each set of combustion device includes a gas burner, an air disc valve, a needle valve and a pressure control valve, which are mounted on both sides of the furnace body.
The old sand that enters the roaster is slowly advanced by boiling and heated by gas flowing in the opposite direction. In the middle of the furnace, the flame and heat from the two burners are mixed with the sand stream, heating the sand to more than 650ºC and burning the resin film on the surface. Finally, the hot sand is discharged from the sand outlet into the cooling bed.
3, cooling bed
Body dimension a long box body, equipped with a hood bed plate will be divided into the upper and lower two rooms, the upper boiling chamber, bellows. A water jacket is arranged on both sides of the outer wall of the box body, and a tubular water cooler is arranged inside. Outside the box are fans and air ducts.
After entering the cooling bed, the hot sand is first air-cooled, then air-cooled + water-cooled, and then flows out from the front end.
4. Control and adjustment in operation
The burning condition and sand condition in the roaster should be controlled and adjusted during operation.
1) Combustion condition
Burner flame should be stable not flashing, furnace temperature to meet the process requirements.
(1) The flame can be directly observed through the observation hole and the ignition hole. The flame is unstable, and the air pressure, secondary air and boiling air pressure should be adjusted.
(2) furnace temperature control
Two temperature gauges on the control panel show the temperature of gas and sand in the middle part of the furnace before discharge. The recommended control scope is as follows:
Furnace temperature: better range of 780-820ºC, allow short time fluctuation range of 750-850ºC.
Sand temperature: a better range of 630-670ºC, allowing short time fluctuation range of 610-700ºC.
In actual operation, if the amount of old sand added into the furnace is large and the productivity is in the upper limit, the furnace temperature should be increased by 10 ~ 20ºC. In addition, the temperature in the furnace should be adjusted according to the quality of reclaimed sand.
Before the temperature approaches the limit, it should be adjusted in time to enhance or reduce the combustion intensity.
2) Sand condition
When running, it is necessary to keep the sand layer boiling well and the sand quantity is basically constant. Only good boiling, sand and heat can be good heat exchange, can be implemented from the feed end to the discharge end of the flow; Only constant sand quantity can protect stable furnace condition and realize continuous production.
(1) Boiling good judgment;
A after the boiling fan is turned on, the sand on the whole sand surface moves one after another without any static place;
B feed in boiling state. After boiling stops, the sand layer is flat or slightly inclined, and there is no obvious accumulation of sand at the feed end.
(2) Factors affecting boiling:
A Fan air volume and pressure: corresponding to a certain height of sand layer, need a certain range of wind pressure. The height of sand in the furnace of this equipment is controlled between 280-340mm, and the corresponding bellows pressure is about 3.8-4.5kpa when boiling. The air volume and wind pressure should not be too large, otherwise the boiling is fierce, the furnace gas volume increases, and the heat brought out also increases.
B feeding method and feed quantity: must be in boiling state uniform feeding, and feed quantity to be appropriate, otherwise it will cause local boiling bad.
(3) observation and control of boiling condition and sand layer height;
A directly observe the boiling condition and sand layer change in the furnace through the observation hole and ignition hole;
B Observe whether the pressure gauge of the bellows is stable in a certain range of 3.8-4.5kpa. If the pressure gradually decreases or increases, it indicates that the sand layer height is decreasing or increasing. If it is found that boiling is not good, it should be checked, such as checking whether the air door of the fan has changed, etc.; If the sand layer is found to be high or low, the sand gate can be opened or closed small; If bellows pressure is lower than 3.0kpa should not continue to work, should stop the furnace to check the cause of sand layer reduction.
5, the furnace
The order is as follows:
(1) Feed machine stop oil pump stop boiling fan, combustion fan.
(2) Turn off the cooling fan and stop the spiral feeder, and turn off the cooling water valve after a few minutes.
(3) Stop the dust removal fan.
6. Special tips
(1) It is strictly forbidden to use the coated sand without heating hardening (including the scattered sand when using, unqualified coated sand, from the thermal coated device to clean out the adhesive material, etc.), into the production line, the production line can not use the wet old sand, otherwise it will cause screen blocking, sand bucket hanging sand and feed fluctuations and other problems.
(2) After the burner is lit and before the sand layer in the furnace is boiling, the flame should not be too large and too long. It should be warned that because the flame is too large and too long, the strong scouring of the sand layer will expose the hood and the boiling bed plate, and lead to a large amount of sand flowing into the bellows.
(3) the starting and closing sequence of boiling fan and feeder must be strictly implemented. When starting, the boiling fan should be opened first. After boiling stability (about 10-30 seconds), the feeder should be opened. When stopping, stop the feeder first and then stop the boiling fan. If only open the feeder or open the feeder or stop the boiling fan first, the old sand may accumulate at one end of the furnace, which can not boil and the baking furnace can not work normally.
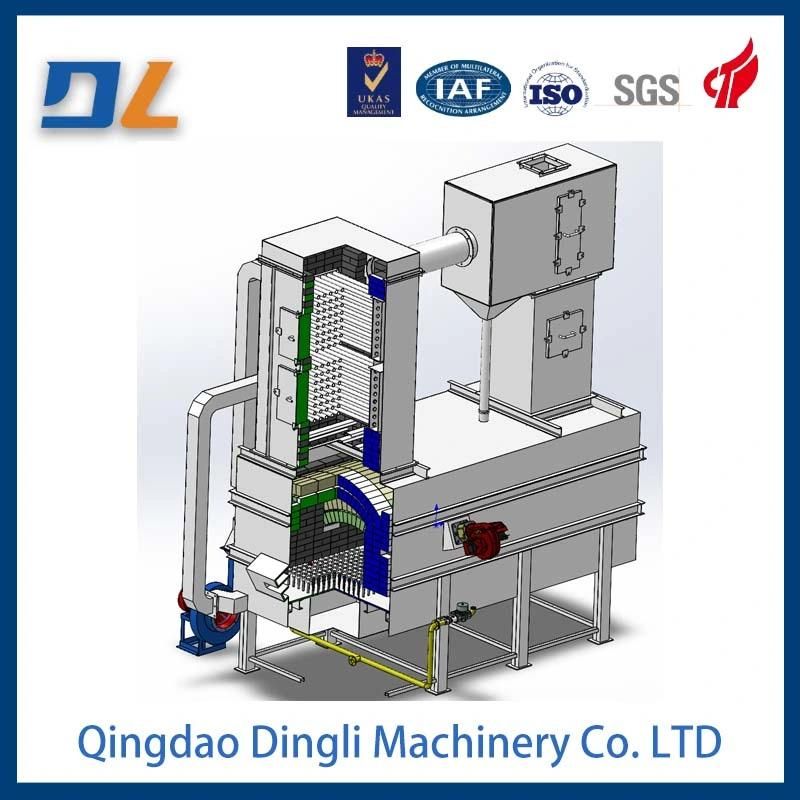
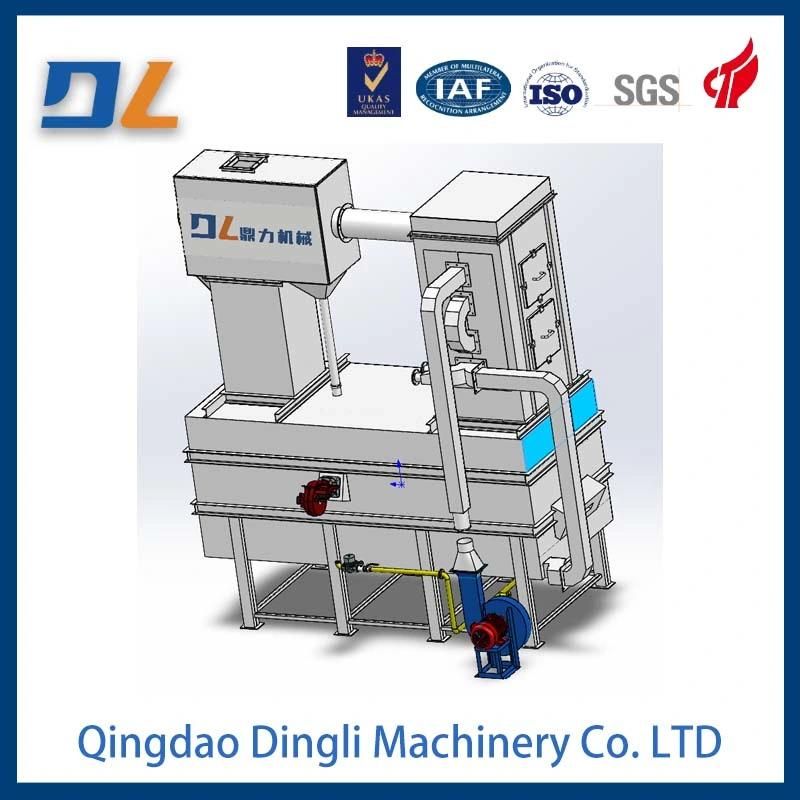
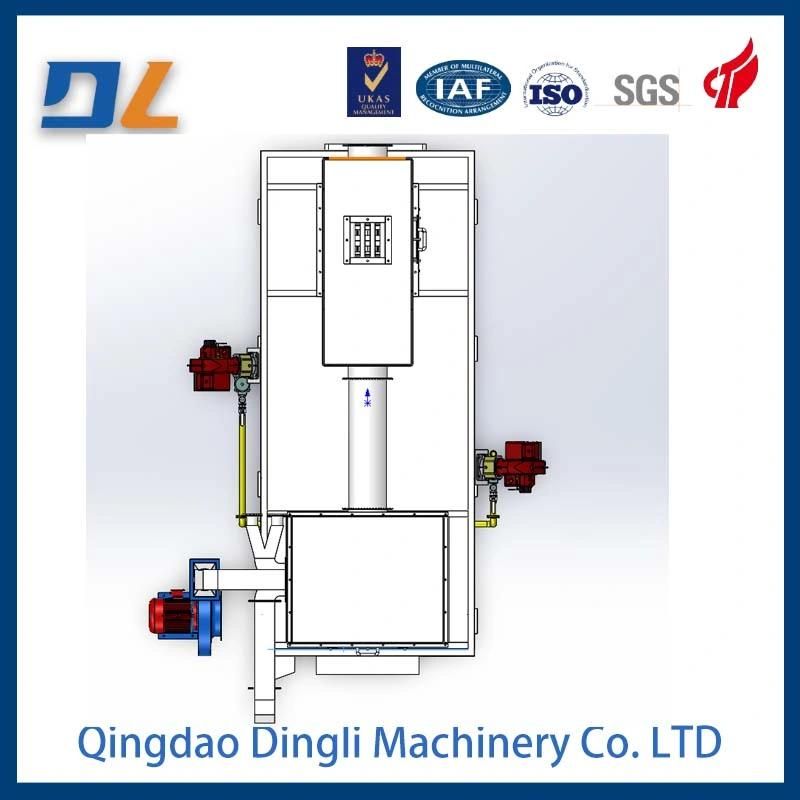
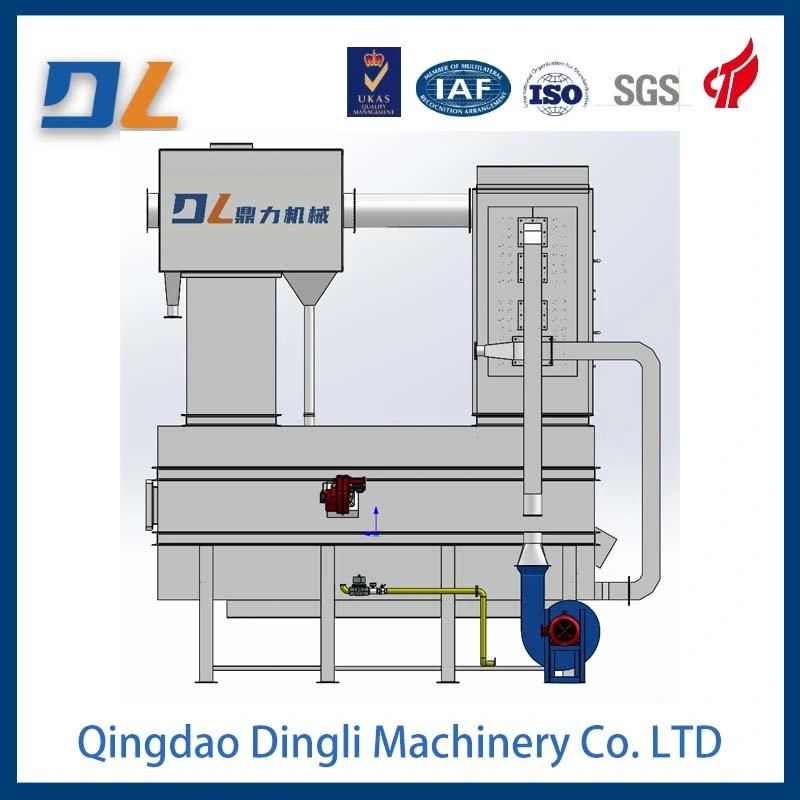
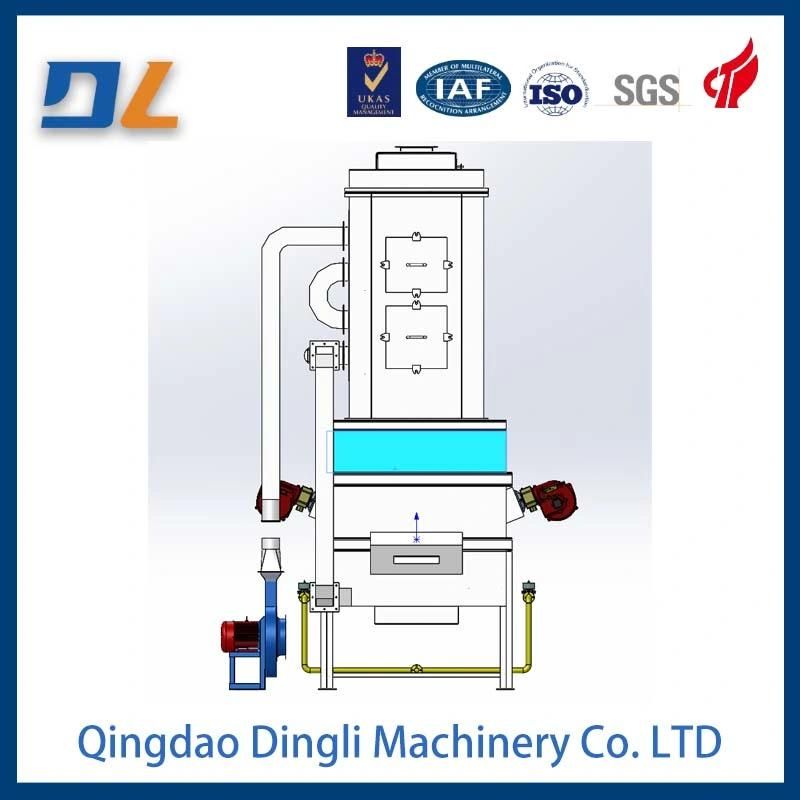